A Comprehensive Overview to the Process and Benefits of Plastic Extrusion
In the large realm of manufacturing, plastic extrusion emerges as a necessary and extremely reliable process. Translating raw plastic into constant accounts, it deals with a variety of industries with its impressive adaptability. This guide intends to clarify the complex steps associated with this technique, the sorts of plastic appropriate for extrusion, and the game-changing advantages it offers the industry. The following conversation guarantees to unravel the real-world effects of this transformative process.
Understanding the Basics of Plastic Extrusion
While it might show up facility initially look, the procedure of plastic extrusion is fundamentally straightforward - plastic extrusion. It is a high-volume manufacturing method in which raw plastic is melted and formed right into a constant account. The process begins with the feeding of plastic product, in the kind of granules, powders, or pellets, into a warmed barrel. The plastic is then thawed using a mix of heat and shear, applied by a turning screw. When the molten plastic reaches the end of the barrel, it is forced through a small opening referred to as a die, forming it right into a preferred type. The shaped plastic is after that cooled down, solidified, and cut into wanted sizes, completing the process.
The Technical Process of Plastic Extrusion Explained
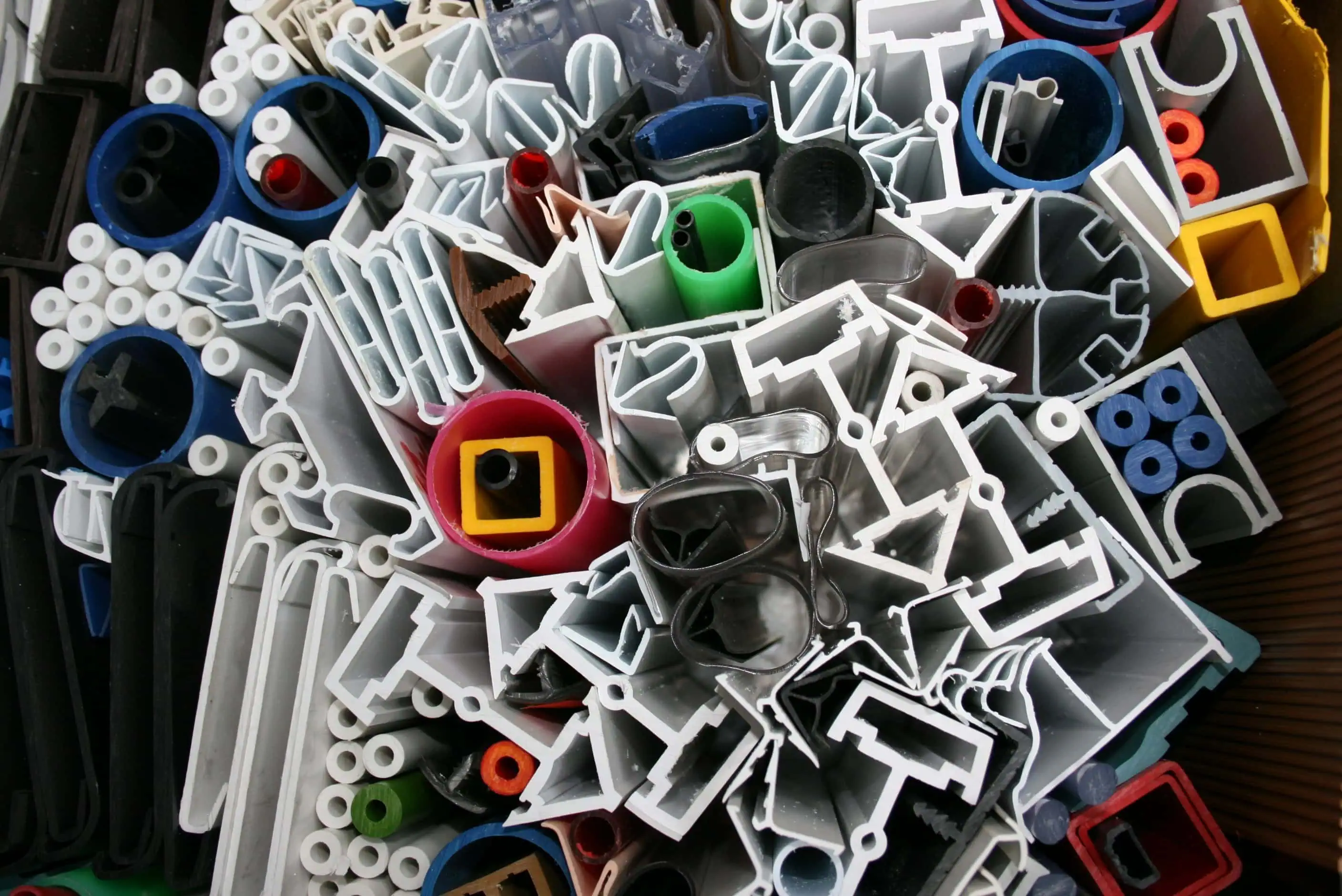
Sorts Of Plastic Suitable for Extrusion
The selection of the ideal type of plastic is a crucial aspect of the extrusion procedure. Various plastics supply special properties, making them extra fit to particular applications. Comprehending these plastic types can substantially enhance the extrusion procedure.
Comparing Plastic Extrusion to Various Other Plastic Forming Techniques
Comprehending the types of plastic ideal for extrusion leads the way for a broader conversation on just how plastic extrusion stacks up versus other plastic creating methods. These include injection molding, strike molding, and thermoforming. Each approach has its distinct usages and benefits. Injection molding, for circumstances, is excellent for producing detailed parts, while strike molding is perfect for hollow items like containers. Thermoforming excels at forming shallow or huge components. Nonetheless, plastic extrusion is unmatched when it comes to developing continual accounts, such as gaskets, pipelines, and seals. It additionally enables a consistent cross-section along the size of the item. Therefore, the selection of approach largely depends on the end-product requirements and specs.
Trick Advantages of Plastic Extrusion in Manufacturing
In the realm of manufacturing, plastic extrusion provides lots of substantial benefits. One remarkable advantage is the cost-effectiveness of the process, that makes it a financially enticing manufacturing technique. Furthermore, this technique provides premium item versatility and enhanced production rate, consequently enhancing overall manufacturing performance.
Cost-efficient Manufacturing Technique
Plastic extrusion jumps to the forefront as an economical production approach in manufacturing. This process attracts attention for its capability to produce high quantities of material swiftly and efficiently, supplying producers with substantial savings. The key expense benefit is the ability to make use of more economical raw materials. Extrusion utilizes thermoplastic products, which are less pricey compared to steels or porcelains. Further, the extrusion process itself is reasonably easy, reducing labor prices. Additionally, plastic extrusion needs much less energy than standard manufacturing approaches, adding to reduced operational expenses. The process additionally minimizes waste, as any type of excess or malfunctioning materials can be reused and recycled, providing another layer of cost-effectiveness. Generally, the economic advantages make plastic extrusion a highly attractive option in the production market.
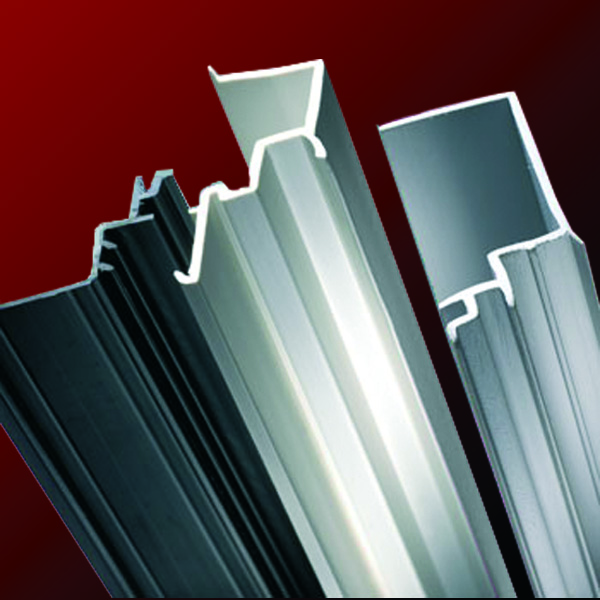
Superior Product Versatility
Beyond the cost-effectiveness of plastic extrusion, one more significant benefit in producing lies in its premium product adaptability. This makes plastic extrusion an optimal solution for markets that require tailored plastic elements, such as vehicle, building, and product packaging. In essence, plastic extrusion's item versatility promotes advancement Resources while boosting functional effectiveness.
Improved Production Speed
A substantial advantage of plastic extrusion depends on its improved manufacturing rate. This production here procedure permits high-volume production in a fairly short time period. It can generating long, continual plastic profiles, which considerably decreases the production time. This high-speed production is especially useful in sectors where huge amounts of plastic parts are needed within tight target dates. Couple of other manufacturing procedures can match the rate of plastic extrusion. In addition, the ability to preserve constant high-speed production without compromising product high quality sets plastic extrusion besides various other techniques. The improved production rate, for that reason, not only allows suppliers to meet high-demand orders but additionally adds to increased effectiveness and cost-effectiveness. This beneficial function of plastic extrusion has made it a preferred selection in many sectors.
Real-world Applications and Effects of Plastic Extrusion
In the realm of manufacturing, the method of plastic extrusion holds profound relevance. The financial benefit of plastic extrusion, largely its cost-effective and high-volume outcome, has reinvented production. The sector is constantly making every effort for innovations in recyclable and naturally degradable materials, suggesting a future where the advantages of plastic extrusion can be maintained without compromising environmental sustainability.
Final thought
In final thought, plastic extrusion is a extremely check this efficient and reliable method of transforming resources into diverse items. It uses many advantages over other plastic forming approaches, consisting of cost-effectiveness, high outcome, minimal waste, and layout adaptability. Its effect is exceptionally felt in various sectors such as construction, automobile, and durable goods, making it a critical procedure in today's manufacturing landscape.
Delving much deeper into the technological process of plastic extrusion, it starts with the choice of the suitable plastic product. Once cooled down, the plastic is reduced right into the needed lengths or wound onto reels if the item is a plastic movie or sheet - plastic extrusion. Contrasting Plastic Extrusion to Other Plastic Forming Methods
Recognizing the kinds of plastic appropriate for extrusion paves the way for a more comprehensive conversation on just how plastic extrusion stacks up versus various other plastic forming methods. Few other manufacturing processes can match the speed of plastic extrusion.